Emission-free into the production of the future: Heat inductively!
In many industrial processes it is important to generate heat. Often, this heat must be available quickly and it must be possible to turn it off just as quickly. In addition, this heat must be distributed evenly and must be able to be controlled dynamically and according to demand. The heating should also require as little energy as possible.
With inductive heating systems from Kendrion you can expect efficient, precise and clean solutions for your heated tools. Find out more now!
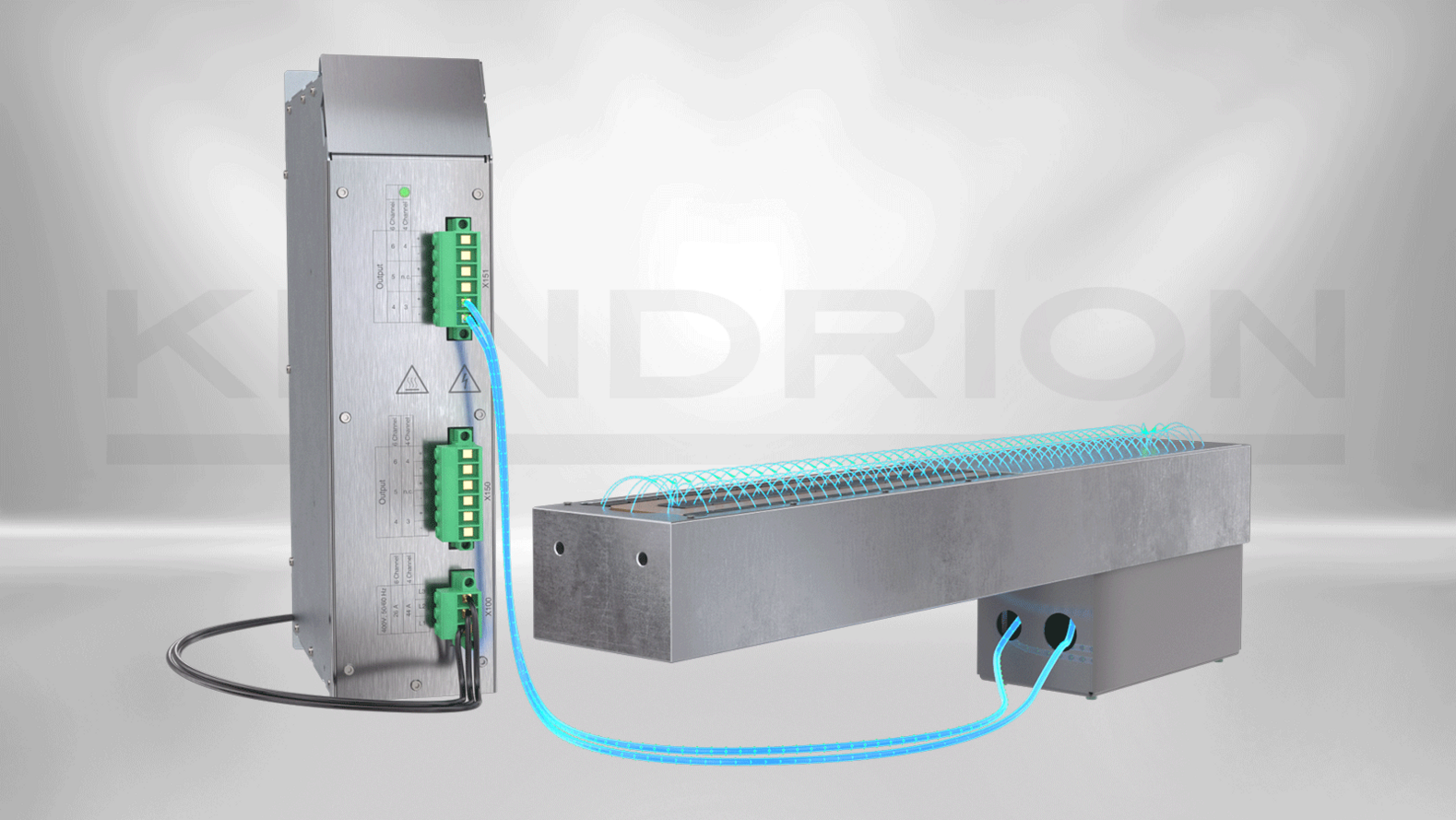
The induction heating systems are designed for manufacturing processes involving electrically generated heat. This includes applications in the plastic processing industry and the textile industry as well as drying processes in the paper industry.
Induction heaters are increasingly being used to heat the tools such as rollers, rolls or cylinders. Not only are they emission-free, they can also provide the heat quickly and switch it off again just as quickly. The inductive heat (up to 250°C) can be evenly distributed and allows dynamic control exactly as required.
Heating according to the eddy current principle
The technology is based on the eddy current principle, in which a magnetic alternating field is generated with the help of high-frequency alternating current, which is introduced into the metal in a defined manner. The resulting eddy current losses generate a thermal power that can be precisely dosed by changing the current flow. Due to the exact controllability of the temperature, the heating process can be reproduced exactly, which ensures a high quality of the process. The temperature is measured directly in the jacket with up to four measuring points. In addition, uniform heating is achieved by a multi-zone design of the surface and roller inductor.
Kendrion offers energy-optimised induction heating systems whose components are precisely matched to each other.
The Kendrion induction generators are designed as a modular system. They consist of a controller and up to 7 stackable induction generators. The controller can be integrated into the control of a machine via a fieldbus interface (e.g. PROFINET®). The control of the individual induction generators and the retrieval of status messages is carried out for all connected generators via the central controller. Depending on the configuration, the controller can also control the heating channels with integrated PID controllers. The units are designed for installation in control cabinets.
DOWNLOAD FLYER - INDUCTIVE HEATING
We support you from technical feasibility to series production!
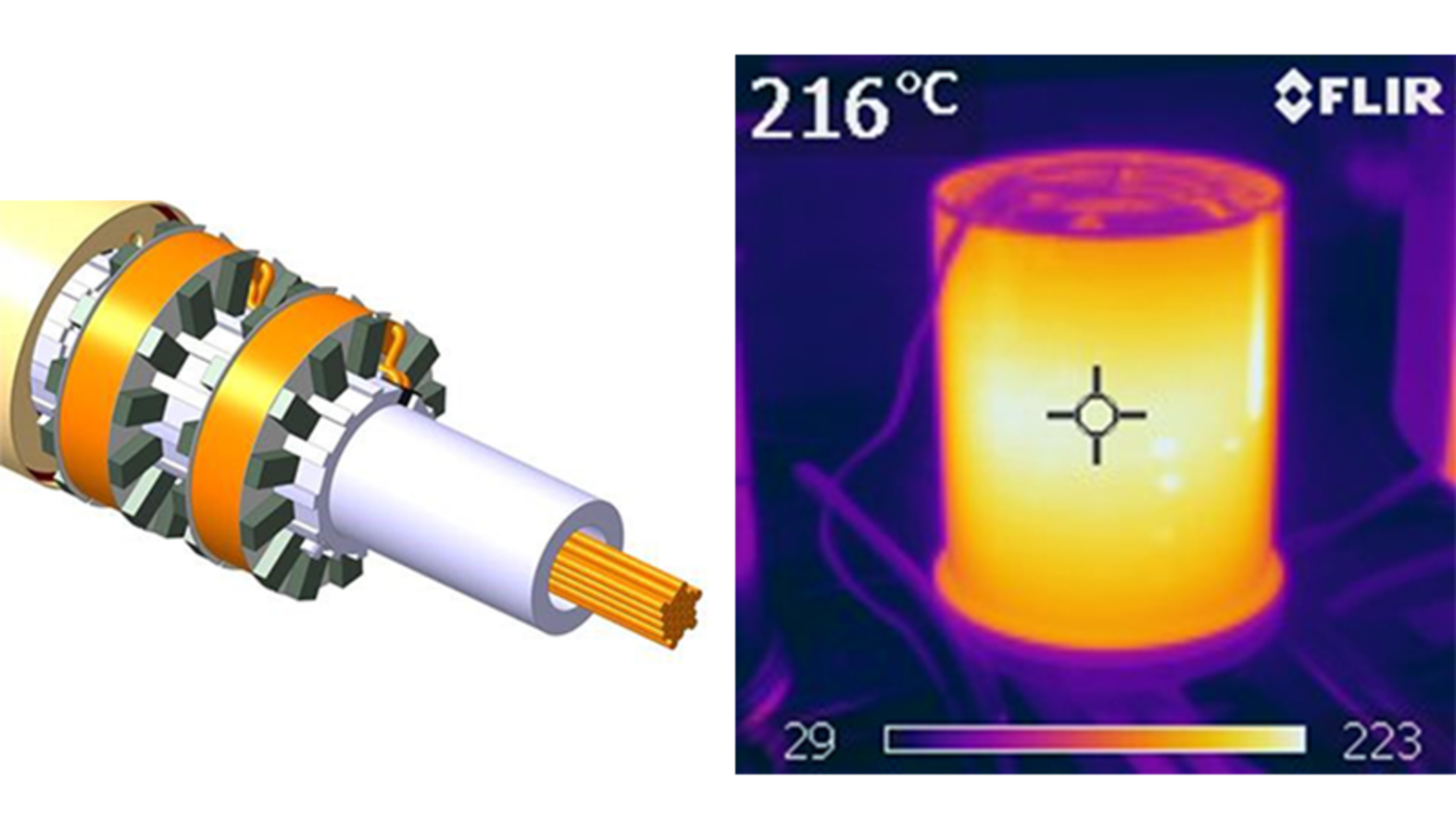
By transforming your processes or plants to induction heating concepts, you are a pioneer and a visionary. Not only does the heating process become more climate-friendly, but above all you achieve an increase in productivity and the quality of the end products.
With Kendrion, you have a partner at your side who not only specializes in the production of induction heaters, but also has extensive expertise in planning and design.
What services does Kendrion offer?
A core competence of Kendrion is numerical simulations of magnetic as well as fluid and thermodynamic processes. With our analysis tools, we can model even complex processes and design them with high precision. This enables us not only to evaluate the success of feasibility studies and preliminary developments, but also to produce concrete designs and samples as well as the final series product.
We are happy to provide support both in an advisory capacity and in the active solution of technical problems.
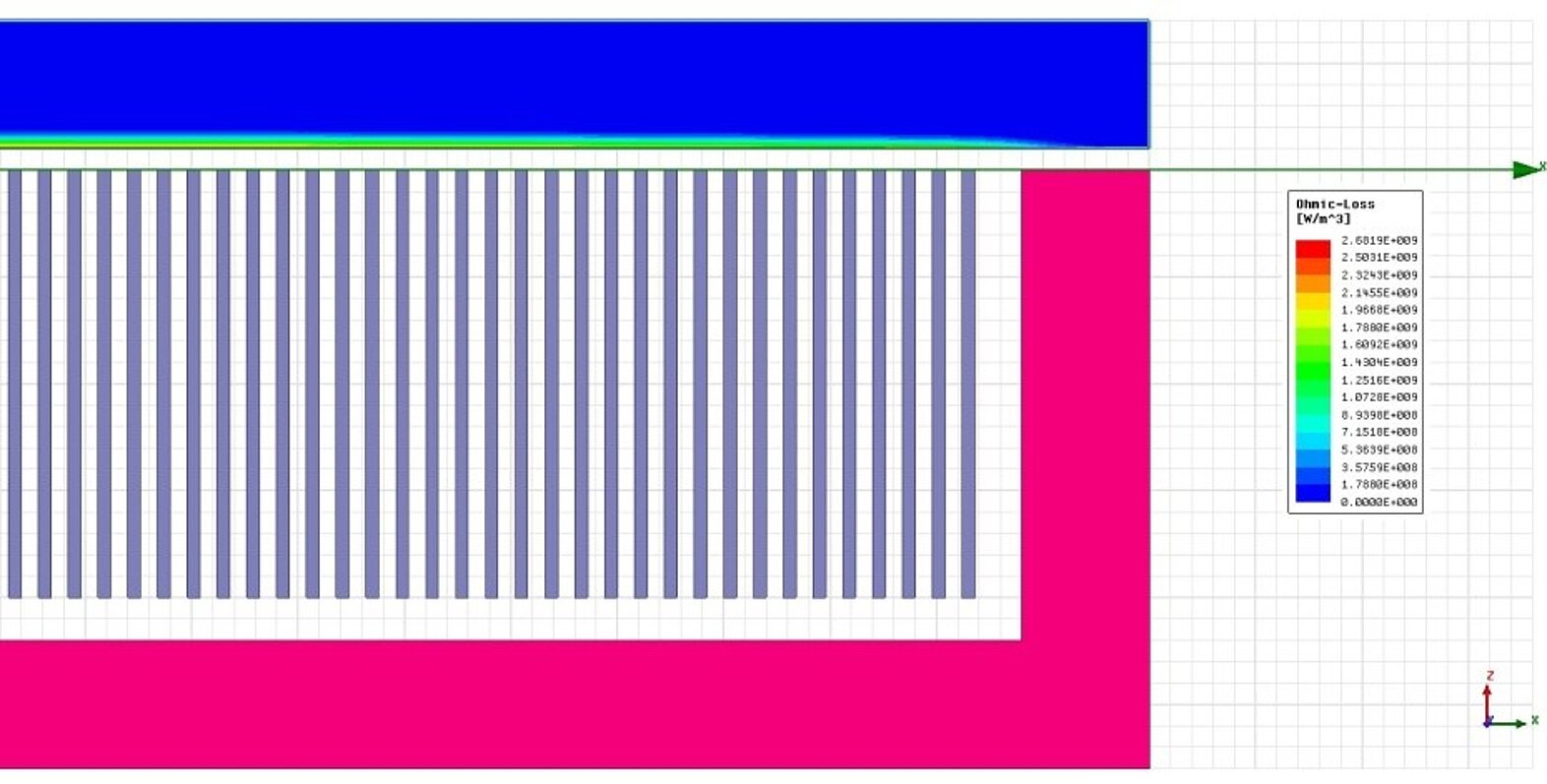
Our services include in detail:
Perform a joint process analysis
Set up functional specifications
Developing conceptual solutions
Creation of the design
Selection and adaptation of the induction generator
Development of the inductor
Realization of the series production
What are the advantages of induction heating?
Temperature, heating time and heat pattern are reproducible. With inductive heating systems, you can convert 90% of the expended energy into usable heat without burning fossil fuels. Process temperatures are reached in a very short time for typical workpieces thanks to high surface power and low masses. By designing the inductors and using multiple heating zones, a very precise surface temperature can be achieved, while the entire heating process can be controlled by induction generators and process control software.
What are the advantages of inductive heating compared to the use of electric heating cartridges?
Induction heating has several advantages over electric cartridge heaters. Firstly, inductive heating offers faster heating, as higher power can be transferred per surface and no thermal contact resistances need to be overcome. Precise temperature control is another advantage, which is particularly beneficial in applications with specific temperature requirements. In addition, induction heating often requires less maintenance due to fewer moving parts (e.g. no slip rings required), and maintenance itself is much easier as the inductors are more accessible. There is no need for the heating cartridges to get stuck in the bores or for poor heat transfer. Last but not least, this method minimises the risk of overheating and reduces the thermal load on other components, resulting in an overall more reliable and efficient heat transfer.
What are the advantages of induction heating compared to the use of gas heaters?
Induction heating offers a number of advantages compared to gas heating systems. The main advantage is that this technology can reduce energy consumption by up to 50%. The direct generation of heat in the workpiece enables efficient energy transfer and minimises losses. By dispensing with gas as a fuel, CO2 emissions can be minimised, resulting in a solution that is not only cost-efficient but also environmentally friendly. The precise controllability of induction heating also makes it possible to regulate the output individually from 0 - 100% in 1% increments. This leads to an exact adjustment of the heating parameters and thus to improved production processes and quality controls in industrial processes. In contrast to gas heating systems, induction heating eliminates potential safety risks such as gas leaks or open flames, which minimises operating hazards and improves overall safety in the workplace.
What are the advantages of induction heating compared to the use of thermal oil heaters?
Induction heating offers several advantages over thermal oil heaters. By generating heat directly in the material to be heated, it is more energy efficient as the energy losses caused by heating the oil in thermal oil heating systems are minimised. In addition, there are no heat losses from oil pipes, which further increases overall efficiency. Induction heating systems can be controlled much more precisely (from 0 - 100% in 1% increments) and enable individual control of specific areas, such as a roller, that are to be heated. Since higher power can be transmitted per area and no thermal contact resistances have to be overcome, faster heating is possible. Another advantage is the compactness of inductive heating systems compared to thermal oil heating systems. The absence of large temperature control units or pipework makes them particularly suitable for systems with limited space. Regular oil changes are no longer necessary, waste is avoided and maintenance costs are reduced, thus minimising overall operating costs. In addition, machines are not contaminated by leaking oil and the risk of injury is significantly reduced.