We develop customized brakes for AGVs from Bastian Solutions
If the driver becomes obsolete, then the space for the seat and cab can also be saved. Bastian Solutions, a US material handling system integrator and manufacturer from Toyota Industries Corporation, came to this conclusion when developing a new autonomous forklift truck. The shorter length and shorter wheelbase not only make the truck lighter and more maneuverable, but also have a significant impact on its braking behavior and tipping safety, especially when loaded. It was at this point in the project that we as a brake specialists came into play. Together with our customer, the experts developed a customized brake solution that meets all the requirements and special features of this application.
"On the one hand, our requirements specification included a very narrow braking torque tolerance," explains Dr. Stefan Weigelt, Head of Customer-Specific Development at Kendrion INTORQ in Aerzen. "Bastian Solutions also had special specifications for the switching times of our brakes, the tolerable emergency stop energies and the minimum possible number of emergency stops." The particularly high requirements for the braking torque tolerances result from the shortened vehicle design. The minimum torque must ensure compliance with the maximum braking distance in accordance with legal requirements. On the other hand, the maximum torque is only slightly higher in order to ensure the tipping safety of the vehicle in case of an emergency stop with increased load capacity.
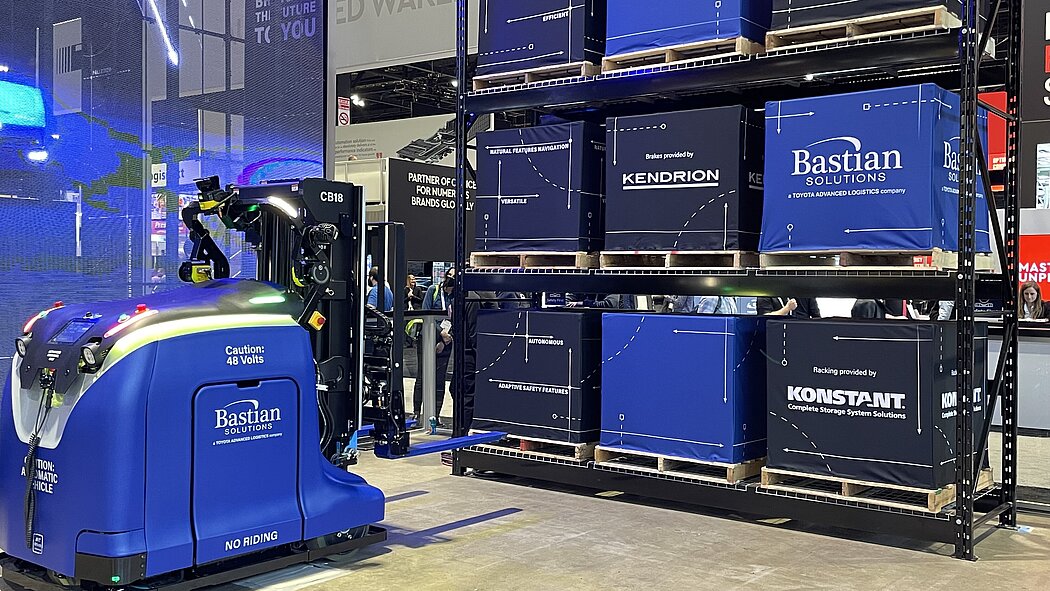
"Our development department in Aerzen worked out the right solution together with Bastian Solutions," says Stefan Weigelt, describing the process. "Based on the technical data of the automated guided forklift (AGF), such as drive wheel diameter, gear ratio and efficiency of the gearbox, we determined the parameters for an optimum brake design with which we can reliably meet the required braking torques." The customized brake is based on our INTORQ BFK557 model in size 12. The modifications made by Stefan Weigelt's team included adjusting the spring force and selecting and qualifying an appropriate friction system, consisting of the rotor with a friction lining suitable for the special requirements and the matching counter friction surfaces.
Six engineers are currently involved in the customer-specific development of add-on brakes at the Aerzen site. Based on our brake series and existing technologies, the team develops customized solutions for the intralogistics, machine building, medical technology and wind power sectors, among others. The modifications that are created here range from simple adaptations, for example to the power supply, to a special torque specification, through to geometrically highly modified brakes for special installation spaces. "Kendrion has extensive expertise in analyzing the requirements of an application," summarizes Stefan Weigelt. "We develop the corresponding specifications together with our customers and design individual solutions on this basis."
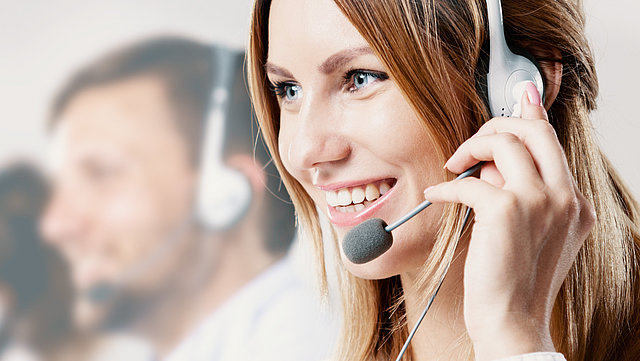